On Track Railroad Laser Additive Repair Manganese Steel
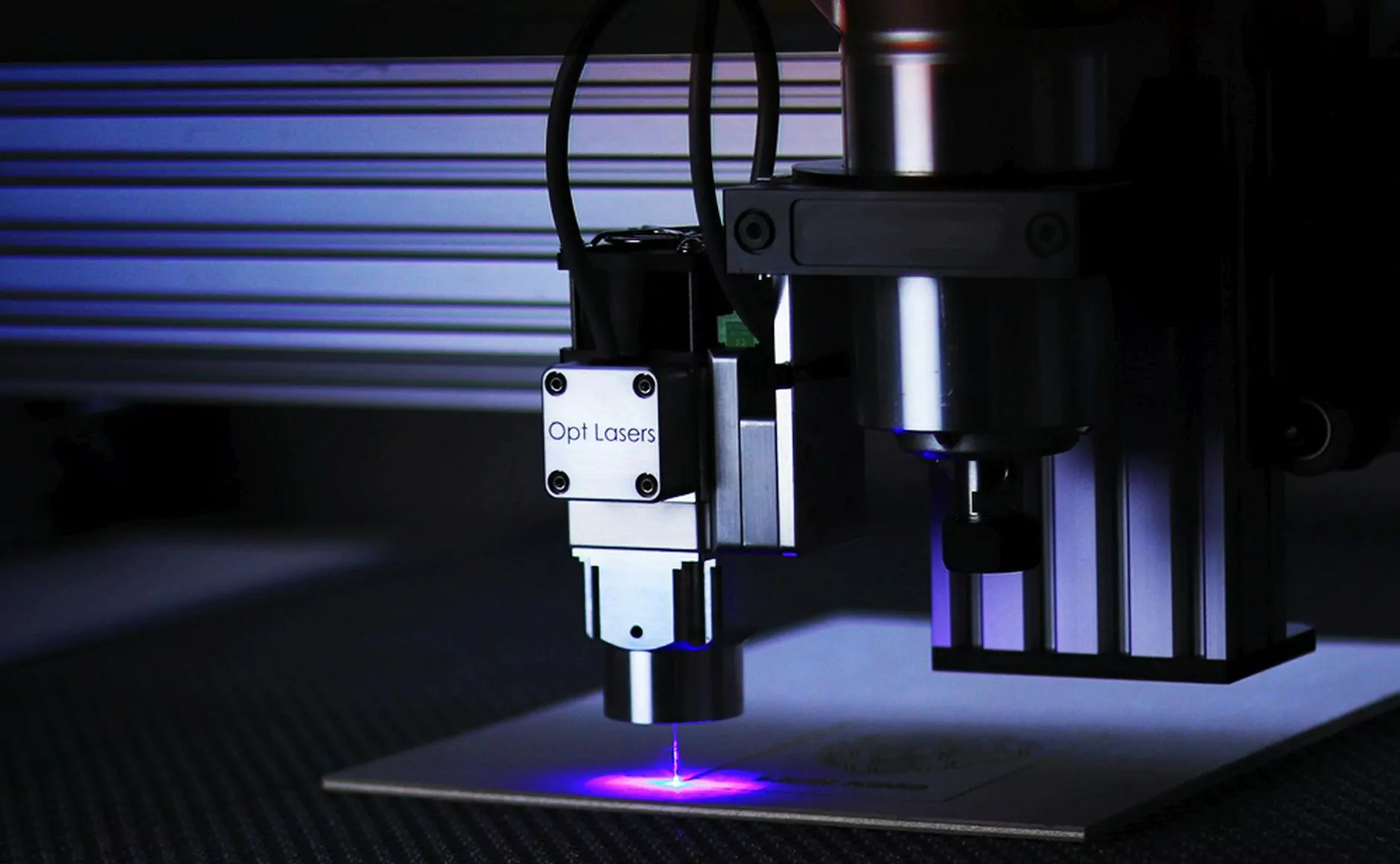
Revolutionizing Railroad Track Maintenance with Laser Additive Repair Technology
Welcome to Powder Keg, a leading provider of advanced solutions for the Business and Consumer Services industry. In this article, we will shed light on our groundbreaking laser additive repair technology, specifically designed for repairing manganese steel components on railroad tracks. With our cutting-edge process, we revolutionize the way railway infrastructure is maintained, ensuring enhanced durability and longevity.
The Importance of Manganese Steel in Railroad Tracks
Railroad tracks are subjected to immense stress and wear due to the heavy loads and constant train movements. To withstand such demanding conditions, these tracks often incorporate manganese steel components. Manganese steel is renowned for its exceptional toughness, high tensile strength, and resistance to abrasion, making it an ideal material choice for railway applications.
The Challenge of Repairing Manganese Steel Components
Over time, even the most durable materials like manganese steel can experience wear, fatigue, and damage. Until recently, repairing manganese steel components on railroad tracks was a complex and time-consuming task. Traditional repair methods often resulted in extended downtime and costly replacements, adversely affecting the efficiency of railway operations.
Introducing Laser Additive Repair Technology
At Powder Keg, we have revolutionized the repair process through our state-of-the-art laser additive technology. This innovative method allows us to precisely repair damaged or worn-out manganese steel components on railroad tracks, extending their service life and maintaining track integrity.
The Advantages of Laser Additive Repair Technology
1. Precision and Accuracy
Our laser additive repair technology ensures precise and accurate repairs, as it selectively melts and fuses the exact amount of compatible material onto the damaged area. This eliminates the risk of over or under-repairing, resulting in optimal track performance.
2. Enhanced Durability
By using laser additive repair technology, we are able to restore the original integrity and strength of manganese steel components. The repaired areas exhibit exceptional resistance to wear, impact, and other forms of damage, ensuring a longer lifespan for the tracks.
3. Reduced Downtime
Unlike traditional repair methods, laser additive repair reduces downtime significantly. With our advanced process, repairs can be carried out swiftly and efficiently, minimizing disruptions to railway operations and allowing trains to get back on track in no time.
4. Cost Savings
Investing in laser additive repair technology proves to be cost-effective in the long run. By avoiding expensive replacements and reducing maintenance cycles, railway authorities can save substantial costs while ensuring reliable and safe track infrastructure.
5. Environmentally Friendly
Being an environmentally conscious company, Powder Keg is proud to offer a repair solution that minimizes material waste. Laser additive repair technology targets only the damaged areas, resulting in minimal material consumption and reducing our carbon footprint.
Choose Powder Keg for Advanced Railway Track Maintenance
With our extensive expertise in laser additive repair technology, Powder Keg is the ideal partner for ensuring the longevity and performance of your railway track infrastructure. Our team of highly skilled technicians, equipped with state-of-the-art equipment, is dedicated to delivering exceptional results and exceeding your expectations.
Don't compromise on the safety, efficiency, and reliability of your railroad tracks. Contact Powder Keg today to learn more about our laser additive repair technology and how it can benefit your railway operations. Trust us to keep your tracks "on track"!