Laser Cladding Cast Iron
Sheet Metal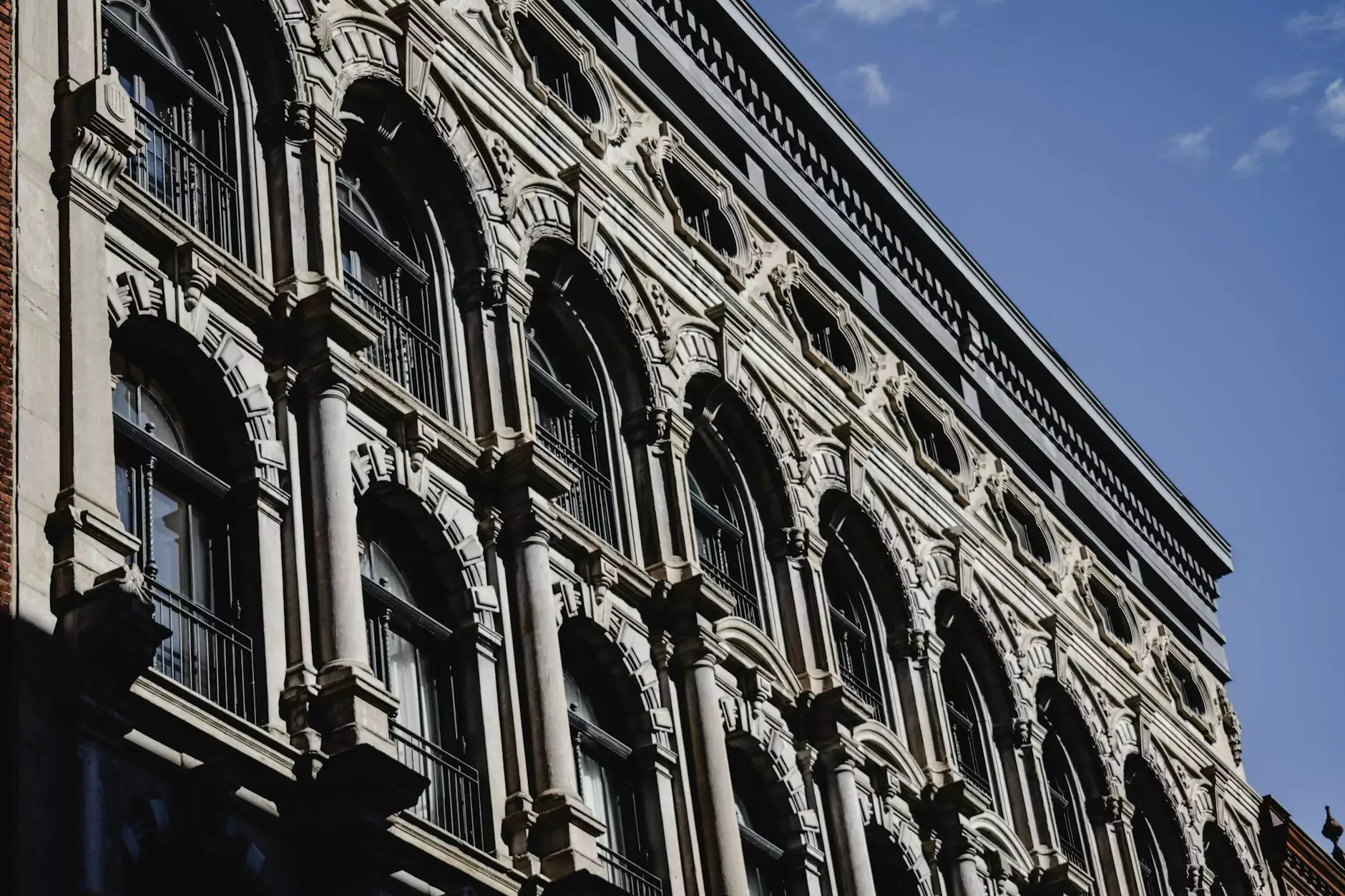
Welcome to Powder Keg's comprehensive guide on laser cladding for cast iron applications. As a leader in the Business and Consumer Services industry, we are dedicated to providing you with high-quality information that will help you understand the advantages of laser cladding and how it can benefit your business.
What is Laser Cladding?
Laser cladding, also known as laser metal deposition (LMD) or laser engineered net shaping (LENS), is a cutting-edge technology used to enhance the properties of cast iron components. It involves the application of a laser beam to deposit a layer of material onto the surface of the cast iron, resulting in improved durability, strength, and wear resistance.
Benefits of Laser Cladding for Cast Iron
Laser cladding offers numerous advantages for cast iron applications across various industries:
1. Enhanced Durability
By adding a layer of specialized material through laser cladding, cast iron components can achieve superior durability, allowing them to withstand harsh operating conditions, high temperatures, and corrosive environments.
2. Increased Strength
Laser cladding ensures a strong bond between the deposited material and the cast iron substrate, resulting in improved structural integrity and overall strength. This makes laser-clad cast iron components suitable for demanding applications that require high strength and resistance to mechanical stress.
3. Improved Wear Resistance
The laser-clad layer provides increased wear resistance to the cast iron surface, reducing the rate of wear and extending the lifespan of components. This makes laser cladding an ideal solution for applications where abrasion, erosion, and friction are prevalent.
4. Precision and Versatility
With laser cladding, it is possible to precisely control the composition and thickness of the deposited material, allowing for customization based on specific requirements. This versatility makes laser cladding suitable for a wide range of cast iron components in industries such as automotive, aerospace, oil and gas, and more.
5. Cost-Effective Solution
Laser cladding can help businesses save costs by extending the service life of cast iron components, reducing the need for frequent replacements. Additionally, the process is highly efficient and can be automated, leading to improved productivity and reduced labor costs.
Laser Cladding Process
The laser cladding process involves several key steps:
1. Surface Preparation
Prior to laser cladding, the surface of the cast iron component needs to be properly cleaned and prepared. This ensures good adhesion between the substrate and the deposited material.
2. Material Selection
The choice of material for laser cladding depends on the application requirements. Various materials, such as nickel-based alloys, cobalt-based alloys, and carbides, can be used to enhance specific properties of the cast iron, such as corrosion resistance or hardness.
3. Laser Beam Application
A high-power laser beam is directed onto the cast iron surface, melting both the substrate and the powdered material. The molten material then solidifies, forming a metallurgical bond with the cast iron.
4. Post-Processing and Finishing
After laser cladding, the component may undergo additional processes such as machining, grinding, or polishing to achieve the desired dimensions, surface roughness, and overall finish.
Applications of Laser Cladding for Cast Iron
Laser cladding can be applied to various cast iron components, including but not limited to:
- Cylinder liners
- Machine tool components
- Valve seats and guides
- Pump impellers
- Engine blocks and heads
- Extruder screws
- Rolls and molds
These applications are found in industries such as automotive, aerospace, oil and gas, power generation, and many more.
The Powder Keg Advantage
As a trusted provider of laser cladding services, Powder Keg offers several advantages:
1. Expertise and Experience
Our team of skilled professionals has extensive experience in laser cladding for cast iron applications. We possess in-depth knowledge of materials, processes, and industry standards, ensuring the highest quality results.
2. State-of-the-Art Equipment
At Powder Keg, we invest in cutting-edge laser cladding equipment to deliver precise and efficient results. Our advanced technology allows for greater control over the cladding parameters, resulting in superior outcomes.
3. Customized Solutions
We understand that each project has unique requirements. Our team works closely with clients to develop tailored laser cladding solutions that meet their specific needs, ensuring optimal performance and cost-effectiveness.
4. Quality Assurance
Powder Keg is committed to achieving the highest quality standards. We follow strict quality control procedures throughout the laser cladding process to ensure consistency, reliability, and customer satisfaction.
With Powder Keg's expertise in laser cladding for cast iron, you can elevate the performance and durability of your components, leading to improved productivity, reduced downtime, and increased cost savings.
Contact Powder Keg today to learn more about how laser cladding can benefit your business!